Key Takeaways:
- Shifting federal policies and resource constraints are creating uncertainty around the future of workplace safety regulation.
- Leadership changes at the Department of Labor and OSHA offer potential for more responsive and balanced safety oversight.
- Safety leaders must stay engaged with frontline realities to identify gaps between policy and practice.
- Traditional lagging indicators like injury rates are no longer sufficient — modern safety demands proactive risk assessment and engagement.
- Continuous improvement and systems thinking are essential for building resilient safety cultures in uncertain times.
Introduction
Recent regulatory developments have left many in the safety community asking important questions about what comes next.
Significant workforce reductions at the Centers for Disease Control and Prevention (CDC) are impacting the operations of NIOSH, the National Institute for Occupational Safety and Health. As the primary research body that informs OSHA’s regulatory actions, any shift in NIOSH’s capacity could have wide-ranging effects — not only on occupational health research but on standard-setting and technical guidance across industries.
Similarly, ongoing resource constraints within OSHA have raised concerns about the agency’s ability to effectively fulfill its regulatory and enforcement mission. With systems still operating under outdated structures and limited modernization, there’s a growing recognition that today’s workplace risks require faster, more agile responses than the current regulatory structure can consistently provide.
On a positive note, recent appointments to key positions within the Department of Labor and the Occupational Safety and Health Administration (OSHA) signal a commitment to experienced and balanced leadership.
Lori Chavez-DeRemer, confirmed as the 30th U.S. Secretary of Labor in March 2025, brings a unique blend of business acumen and labor advocacy to the role. Her background as a small business owner and her previous support for pro-labor initiatives suggest a collaborative approach to workplace safety.
Similarly, David Keeling, nominated to lead OSHA, offers extensive experience in occupational safety from his tenure at major corporations like Amazon and UPS. His industry-aligned perspective is anticipated to enhance OSHA's efficiency and responsiveness to workplace safety concerns.
What’s Happening in the Broader Safety Landscape
In response to these recent regulatory developments, several professional organizations have begun to mobilize:
- The American Society of Safety Professionals (ASSP) and the National Safety Council (NSC) have issued early statements and are actively advocating for continued support of health and safety programs at the federal level.
- These groups — alongside others like the American Industrial Hygiene Association (AIHA) — have engaged in outreach to the new Secretary of Labor, the Senate HELP Committee, and other stakeholders, calling for a clarified vision for the future of worker protection and public health research.
- Discussions are also underway around bipartisan efforts to ensure the long-term sustainability of NIOSH’s mission and its role in supporting a competitive, healthy workforce.
Though not all details are public yet, there’s a clear sense of collective alignment forming across the safety community. These efforts reflect a shared belief: that protecting workers and strengthening safety systems is essential — not just as a compliance obligation, but as a pillar of operational resilience and national well-being.
Leading with Resilience: Questions Every Safety Leader Should Be Asking
While the path forward may feel uncertain, the responsibility to protect workers remains unchanged. Organizations that thrive in periods of disruption are those that lead with intention — grounded in their values, committed to continuous improvement, and supported by resilient systems. This moment isn’t just a challenge; it’s an opportunity to reinforce the foundations of safety culture. By leveraging systems thinking, anticipating risk, and investing in people and processes, companies can adapt and lead — regardless of how federal policy evolves.
A helpful starting point is to focus on a few core questions that should anchor any robust safety system:
- Is work happening the way we think it is?
This question challenges assumptions and helps uncover gaps between planned procedures and actual conditions on the ground. It prompts deeper engagement with frontline teams and fosters more accurate situational awareness.
- What tells us that risk is at an acceptable level?
Today's leaders know full well that absence of injury is no longer a reliable indicator of the presence of safety. Leader & Worker engagement through feedback, observation, and risk assessments, with a priority on Fatality Prevention, is driving prevention alongside improvement.
- How are we improving?
True resilience requires momentum. An intentional commitment to improvement supports lessons learned from leader/worker engagement as well as ongoing discovery, where safety improvements alongside adjacent business benefits surface new opportunities and strengthen momentum.
These questions aren’t just theoretical — they’re practical tools for navigating ambiguity with intention. Together, they provide a framework for action that connects leadership to operations, aligns strategy with culture, and reinforces a proactive approach to worker well-being.
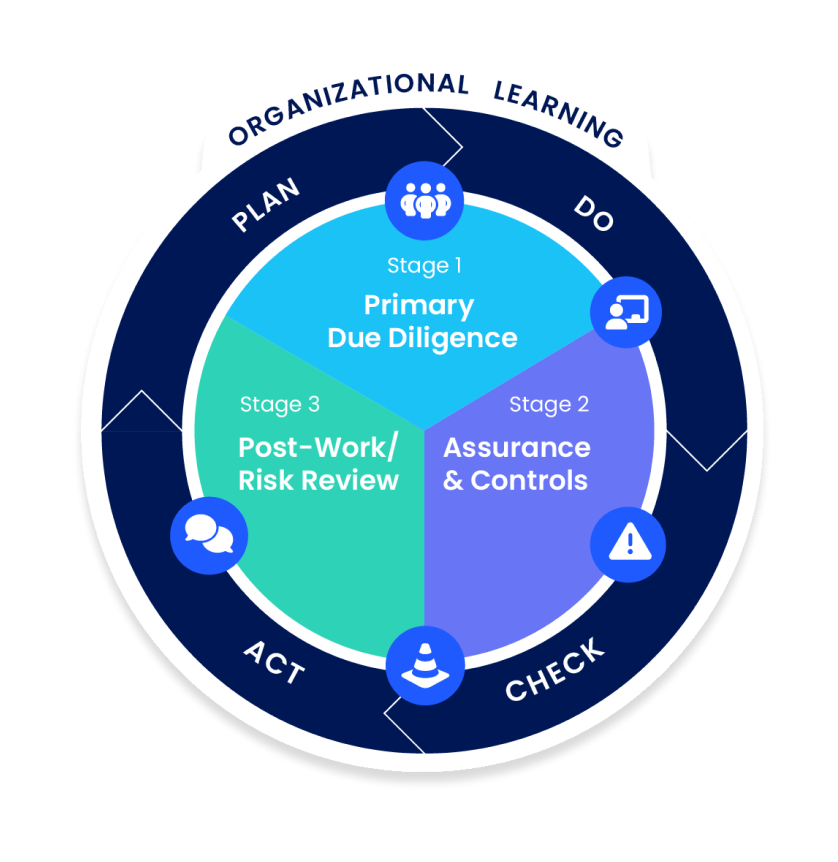
Plan-Do-Check-Act (PDCA): A Framework for Action
The above three questions naturally point toward a structured, repeatable approach for managing safety: one that emphasizes planning, action, reflection, and improvement. That’s where the Plan-Do-Check-Act (PDCA) model comes in.
PDCA provides a practical framework to translate the answers to those questions into day-to-day operations — helping teams move from intent to execution in a consistent, scalable way. Whether you're launching a new initiative or refining an existing program, PDCA offers a roadmap to keep safety systems adaptive, measurable, and aligned with organizational goals. As such, rather than bending with the changeable winds of regulatory pressure, organizations should implement a systems driven cycle of continual improvement for their safety programs as soon as possible.
The Plan-Do-Check-Act (PDCA) continual improvement model is grounded in globally recognized, sound elements of Safety Management Systems. It will allow you to create stable processes for implementing learnings about safety drivers and opportunities that are resilient in the face of external disruptions.
This framework enables organizations to:
- Plan – Assess risks, establish safety goals, and identify system drivers and opportunities for improving safety performance.
- Do – Implement targeted safety improvements as well as proactive and leading interventions.
- Check – Continuously monitor risk and measure performance using tools such as audits and advanced analytics.
- Act – Adjust strategies based on findings, strengthening and refining the safety system through defined coupling points between stakeholders to drive organizational learning.
This structured approach ensures that safety is never static and that organizations involved in work are continually connected in advancing ideas for improvement and evolving alongside new risks, workforce dynamics, and operational demands. This model is a proven and important step towards elevating expectations, improving performance, and creating resiliency for your safety programs in the face of regulatory uncertainty.
Conclusion: How Do We Lead in Times of Uncertainty? Lead Anyway. Let's Go!
In times of uncertainty, the instinct may be to pause and wait for clarity. But for those charged with protecting workers, standing still is not an option. Regardless of what unfolds at the federal level — whether in terms of policy shifts, agency restructuring, or leadership changes — the responsibility to lead remains.
This moment calls for a renewed commitment to fundamentals: understanding how work is really happening, evaluating whether risks are truly under control, and continuously improving the systems that keep people safe. By leaning into proven frameworks like PDCA and staying grounded in clear, operational questions, organizations can lead with intention and resiliency.
The safety community and other industry leaders are not standing by — they’re huddling up. Industry groups are aligning, practitioners are sharing insight, and leadership is emerging from every corner of the field. The message is clear: we lead not because conditions are perfect, but because the work — and the people — matter too much to do anything else.